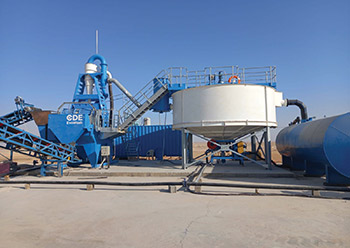
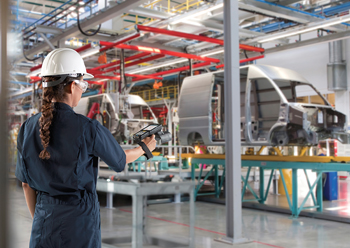
Manufacturers, who were ironically slow to implement a barcoding standard several decades back, have been among the first to embrace radio frequency identification (RFID) technology as they pursue the potential of the Fourth Industrial Revolution (4IR).
Automotive manufacturers, in particular, are adopting this technology. Though fixed industrial scanners can automate barcode scans as inventory moves along production lines and conveyor belts, manufacturers wanted a better way to locate and report on individual items once they left lines – and their facilities. RFID can provide constant visibility to tagged goods that are technically out of sight, removing any uncertainty about the status of each item and increasing accountability for their movements – or stagnation – throughout the supply chain.
![]() |
Wheeler |
This visibility makes it easier to optimise processes, identify bottlenecks in workflows, and report on production and fulfillment processes to key stakeholders, including customers. RFID also makes it easy to confirm the right component is being integrated into the right product, creating serialised as-built records and to quickly locate and pull non-conforming inventory.
In fact, many European auto manufacturers are now mandating their original equipment manufacturer (OEM) suppliers tag every part they ship. This requirement enables the manufacturer to economically automate inbound logistics, including confirmation of receipt at the loading dock and redistribution of parts to the right line, staging or shelf location. It also empowers the automation of intralogistics workflows in factories and warehouses, particularly material and information flow.
As my colleague Darren Russell once said: “By requiring suppliers to mark raw materials and vehicle components with RFID tags in addition to the standard barcode, automotive manufacturers are taking back control of their production processes, even as they program more individualised orders into assembly-line systems in highly automated factories. They can see the right parts are being picked for each order, delivered to the production line at precisely the right time and then installed properly. They can simultaneously direct the installation of parts and inspect the work.”
BEYOND THE LINE
RFID tags aren’t just proving to be fantastic inventory management tools for manufacturers, they’re also providing insights to the process and workflow. For example, a manufacturer can use RFID along with other location technologies to track its material handling equipment. Operations can then see whether a forklift has strayed off course or idled for too long – a signal that there may be something wrong with the larger workflow. Perhaps there was something – or someone – blocking the more efficient route from point A to point B or the materials the operator was asked to retrieve weren’t in the reported location. By tracking material handlers, manufacturers can drive process improvement, eliminating wasted motion, excess time, and opportunities for errors. In a just-in-time environment, every second matters.
![]() |
Boxes being scanned and tagged through a belt conveyor system |
RFID tags can also help manufacturers keep tabs on their inventory as it moves further downstream to distributors or customers, depending on the fulfillment model. They are just as eager to know when something has arrived at its destination as the receiving party. RFID can help improve accountability if something goes missing and helps expedite, even automate, billing processes. Furthermore, RFID tags enable manufacturers to track and report their on-hand inventory. If fixed RFID readers are installed at dock doors, they will know the second something is loaded onto a truck or container, in which case they can deduct it from available stock. They can also send an automatic notification to stakeholders that goods are on the move, much like a barcode but without the manual intervention by a worker. In fact, it’s these benefits that are leading to more prolific RFID tagging among all manufacturers, not just those in the automotive sector.
Coming out of months-long production limitations during the pandemic, food and beverage, pharmaceutical, and consumer packaged goods (CPG) manufacturers are under more pressure than ever to meet tight fulfillment deadlines among a boom in orders. By tagging their assets, they are better positioned to comply with customer demands. Much like air traffic controllers overseeing and orchestrating flights, manufacturers and supply chain stakeholders can see the position of people, equipment, and goods with a refreshing exactness. Better yet, they can take action when they see something moving off course, before there are disastrous consequences.
However, if we’re being real, manufacturers’ rising interest in RFID is also a bit reactive. Though technologists at the core and leaders in automation, machine vison and other advanced technologies, many manufacturers find themselves increasingly following the lead of their customers when it comes to RFID.
TURNING THE TABLES
Much of the Supply Chain 4.0 modeling now taking hold has been initiated by retailers, healthcare providers, governments and even hospitality industry leaders aiming to regain control over their supply chains and stockrooms. They are the ones seeking real-time visibility into inventory location and asking to see greater automation in warehouses and distribution centers. They must ensure supply is available when and where they need it, and that’s not something they can accomplish without cooperation from upstream suppliers, shippers, and logistics partners.
Medication availability is one of the leading challenges cited by pharmaceutical industry decision-makers according to a new Zebra study. And approximately 80 per cent of hospital executives plan to automate workflows in the next year to improve supply chain management and make it easier to locate critical equipment and medical assets.
Of course, we know the pain retailers and restauranteurs are facing right now. Shoppers say they often leave stores without making an in-store purchase due to items being out-of-stock. They are also discouraged by the fact that physical inventory doesn’t align with virtual counts. Retail associates are too. That’s why only four-in-10 completely trust retailers to fulfill their orders as promised.
The consensus seems to be that RFID is the best way to get a grasp on inventory and assets in stores, restaurants, hospitals, and hotels, but that requires manufacturers’ participation in solution implementation. The costs of tagging at the source are significantly lower than tagging at the point of sale, as tags can be purchased and applied in bulk during production or packaging as part of the standard process.
More importantly, the payoff of tagging at the source is much greater for all parties, even for lower value items.
Manufacturers have an organic way to track produced goods throughout and outside their facilities. Distributors, warehouse operators, and shippers can install fixed readers that automatically recognise and report when goods come in, are put away, picked, packed, and shipped once again. And both retailers and service providers can give workers handheld RFID readers – or perhaps just RFID sleds attached to mobile computers – to instantly count, locate and report on all goods within the four walls of their own facilities. Autonomous mobile robots (AMRs) can automatically roam the operation, reading tags and verifying their location when wide-area readers aren’t the right fit.
In turn, housekeeping can keep track of linens. Loss prevention teams can keep goods from walking out of stores – or fraudulent goods from coming in. And healthcare providers, pharmacists, first responders and other critical care providers can locate the supplies and equipment they need to keep people healthy and alive.
That builds a strong business for RFID, no matter where you sit in the supply chain. But I would argue the value proposition is strongest for manufacturers. Whether you leverage RFID to keep your operations running smoothly or help your customers smooth out their supply chain flows, you will see customer satisfaction levels increase. Plus, with RFID tags now readable on metal, liquid-based items, and cold chain products (including frozen meat), there’s really no excuse to stick with the status quo.