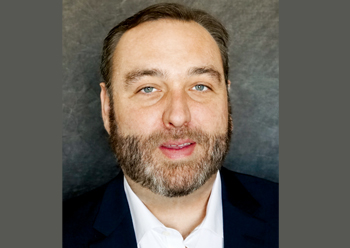
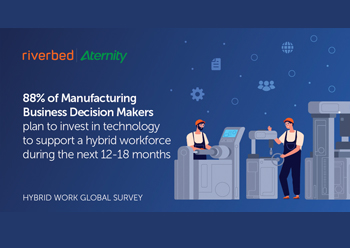
Some 88 per cent of business decision makers (BDMs) in the manufacturing industry say they plan to invest in technology to support a hybrid workforce during the next 12-18 months, says a survey.
The Riverbed|Aternity Hybrid Work Global survey reveals that 51 per cent BDMs in the manufacturing industry believe that half (50 per cent) of their workforce will remain hybrid post-pandemic.
Additionally, the vast majority of manufacturing BDMs (96 per cent) believe a hybrid structure would help them recruit talent and remain competitive.
HYBRID A BUSINESS PRIORITY
Offering a seamless hybrid-working environment is not a nice to have anymore, but a business priority as the manufacturing sector looks to recover from Covid-19. However, only a third (33 per cent) of Manufacturing IT Decision Makers (ITDMs) say their current IT estate is completely prepared to support the demands of long-term hybrid work. This has left 85 per cent of Manufacturing BDMs worried about a disparity in network and application performance for hybrid or remote employees versus in-office employees.
![]() |
Commenting on the report findings, Mena Migally, Regional Vice President, META at Riverbed | Aternity, said: “During the last two years, the pandemic has had a significant impact on the Manufacturing sector across the globe, as businesses have had to shift much of their operations to a remote and hybrid working model. For a sector where employees don’t traditionally work remotely, these changes have presented an opportunity for manufacturers to take a significant leap forward in their digital transformation journey.
“Manufacturers have not only adopted new technologies that will give them a competitive advantage, but increasingly are leveraging visibility and observability solutions to deliver actionable insights that drive business performance and an exceptional digital experience. Especially with the global supply chain disruption, the ability to support a remote workforce can translate to increased productivity as employees can operate from anywhere and at any time. As a result, manufacturers across the META region are working to create environments that will be productive, collaborative and attract the talent that will set their business apart now and into the future.”
HIGH-PERFORMING
The Riverbed | Aternity report revealed that creating sustainable and high-performing hybrid workplaces are critical for business success, and reliant on organisations addressing both human-and technology-related barriers. According to Manufacturing ITDMs, the top five barriers to adopting a sustainable hybrid work model are:
• Expanded security risks (35 per cent);
• Lacking the right technology and equipment in the office (30 per cent);
• Technology disruptions (28 per cent);
• Lacking the right technology in the home set ups (25 per cent); and
• Poor home/remote network performance (24 per cent).
Manufacturing BDMs agree that collaboration and virtual relationship building (31 per cent) is also one of their biggest barriers to adopting hybrid working across their organisation. However, 35 per cent cite poor home/remote network performance as the main reason.
Furthermore, BDMs believe that if we don’t act now, manufacturers will begin to fall behind other sectors. Issues such as Wi-Fi not working properly (46 per cent), the inability for employees to connect to corporate networks (41 per cent) and increased network traffic/bandwidth consumption and unreliable application performance (31 per cent), will all have a huge impact on the ability to provide hybrid working over the next 12-18 months.
To identify and troubleshoot these issues, manufacturers need greater visibility and actionable insights. ITDMs identify the top five challenges with current visibility/monitoring solutions as:
• Too much data and not enough context or actionable insight (39 per cent);
• Lack of unified visibility across the entire technology infrastructure (36 per cent);
• Multiple tools that give conflicting data, delaying root cause analysis and issue resolution (34 per cent);
• Lack of visibility into the availability, performance and usage of cloud resources (34 per cent); and
• Data is not accessible or usable by all who need it (30 per cent).
FUTURE OF MANUFACTURING
The majority of Manufacturing ITDMs (92 per cent) agree that their organisations would benefit from having greater visibility into their networks and systems to identify performance or security risks. And 89 per cent believe there should be more investment into performance and acceleration solutions that will help them to increase productivity and allow them to create the experiences that will attract more talent to the sector.
It’s encouraging that 92 per cent of Manufacturing ITDMs and 88 per cent of BDMs agree and are committed to investing in new technologies to support a hybrid workforce during the next 12-18 months. Their top areas of technology investments will be:
• Updating company-wide hybrid workplace strategies and policies (44 per cent);
• Investing in application or network acceleration solutions (38 per cent);
• Investing in end-user experience and digital experience monitoring solutions (35 per cent);
• Investing in cybersecurity technology and software (34 per cent); and
• Better visibility of network and application performance (33 per cent).
“In 2022, the manufacturing sector must move forward and take positive learnings from the last year of change. By implementing unified observability, full-fidelity visibility and acceleration technologies, they will be able to attract new talent, create new opportunities and build a productive and happy workforce, with hybrid at its core,” concludes Migally.