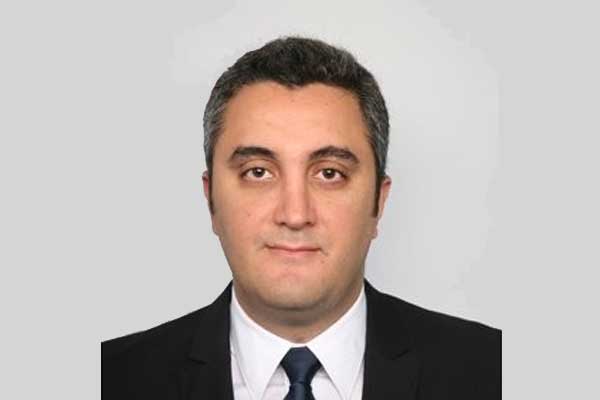
Schneider Electric, a leader in digital transformation of energy management and automation, is highlighting its IoT-enabled, open, interoperable architecture EcoStruxure for oil, gas and petrochemicals solutions at the Abu Dhabi International Petroleum Exhibition & Conference (Adipec), being held in Abu Dhabi, UAE.
Adipec which opened on November 11 will run until tomorrow (November 14) at the Abu Dhabi National Exhibition Centre.
Schneider Electric is showcasing how its IoT-enabled, open, interoperable architecture EcoStruxure for oil, gas and petrochemicals, power and process solutions is helping its oil and gas customers create more value across their enterprises.
Chris Dartnell, president oil and gas segment, Schneider Electric, said: “We have built a strong reputation as an innovative partner to the global oil and gas industry because of our ability to help customers improve returns on CapEx and OpEx spend across the lifecycle of their assets, from design to operations, and across their entire value chain.”
“At Adipec 2019, we will showcase how advanced, digital technologies, like our IoT-enabled EcoStruxure platform, help our customers in the oil and gas and other energy-intensive segments reduce project risks and costs while reaching first production sooner,” he said.
By taking an asset-centric view of the plant across its lifecycle and supply chain, customers can better leverage capital investments upfront to optimize profitability and ROI when the plant begins operating.
Georges El Mir, vice president oil and gas Middle East and Africa, Schneider Electric, said: “Our technologies enable our customers to take a holistic view of their operations to optimize CapEx and OpEx investments.”
“For example, we can help bring down the traditional barriers between power management and process automation systems to help industrial customers solve critical engineering and operating challenges. Because they now have the ability to connect assets that are the centre of their projects with assets that are at the core of their operations across the full lifecycle of their plants, our customers can realise new levels of efficiency and agility, while improving the safety and profitability of their operations,” he added.
As an example of that, Schneider Electric worked closely with a major oil refiner on a greenfield project that unified electrical and automation project design and execution. The scope of the project included the design, delivery and commissioning of the company’s EcoStruxure Foxboro distributed control system, EcoStruxure Triconex safety system and complete electrical distribution system within an e-House enclosure including Schneider Electric Low Voltage and Medium Voltage switchgear and Motor Control Centers, transformers, and Uninterruptible Power Systems (UPS) systems.
The goal of the unified approach was to reduce CapEx spend while optimising the project schedule, enabling improved operations, and documenting best practices for future projects.
According to the customer, CapEx for the project’s control and power systems was reduced by 15 per cent, mainly through a reduction in electrical infrastructure, wiring, cabinets, and labour. The project also successfully set best design practices for future projects.
Overall, Schneider Electric’s technology approach is proven to enable CapEx improvements of 20 per cent on Electrical and Instrumentation projects across the asset lifecycle, downtime reduction of up to 15 per cent, reduction in process energy utilisation of 7-12 per cent and EBITDA improvements of 3-5 per cent pts.
The effectiveness of Schneider Electric’s approach was highlighted in its successful project with BASF, at Beaumont, Texas, in the United States. Schneider Electric supported the world’s largest chemicals company in putting together a new substation and integrated services, as well as equipment for the plant’s main distribution point.
This was made possible with Schneider Electric’s cloud-enabled EcoStruxure Asset Advisor, which provides BASF 24/7 visibility into the health of its critical equipment.
Dartnell said: “Schneider Electric has the unique ability to provide and connect our customers’ power systems, process control and safety systems with leading design, simulation, training, asset management and digital twin solutions.”
“Using a common simulation platform, and connecting things like virtual modelling to real-time operations data, we help customers close the loop between ‘as designed’ and ‘as operating.’ As a result, BASF is now able to continuously monitor 63 assets remotely for analysis; measure and compute more than 100 different variables; provide access to the Asset Advisor Service Bureau; and mitigate risk for the plant’s electrical distribution,” he added.
The company has also recently worked closely with Abu Dhabi National Oil Company (Adnoc) on one of its latest offshore developments. Schneider Electric was brought in as a main electrical equipment supplier to support the installation of six new wellhead towers and an off-shore super complex consisting of six bridge linked platforms.
The objective was to include an Integrated Electrical Architecture from one supplier with Electrical Asset Management to ensure predictive maintenance of capital electrical equipment and use a secured Cyber network with one electrical partner for services, it stated. – TradeArabia News Service